Aerogel Felt as an Energy-Saving Insulation Material in Thermal Pipeline Applications
Table of Contents
Description of Thermal Pipeline
A thermal pipeline refers to the heating pipes that extend from boiler rooms, direct combustion engine rooms, heating centers, etc., transporting heat from heat sources to the thermal entry points of buildings. Multiple heating pipes form a network. With economic development and the promotion of centralized heating policies, the area covered by centralized heating will continue to grow. Such an extensive heating pipeline network requires a robust insulation system to ensure energy efficiency and safety during transportation.
The heating pipelines from the heat source plant to the thermal users are divided into primary and secondary networks. The primary network comprises heating pipelines from the heat source to the thermal station, while the secondary network encompasses pipelines from the thermal station to the thermal users. Typically, the primary network has diameters ranging from DN500 to DN1000, while the secondary network has smaller diameters ranging from DN125 to DN300.
The installation methods for heating pipelines generally include underground and aboveground methods. Underground installation includes trench and direct burial methods, while aboveground installation involves overhead placement. The primary network has a supply water temperature of 120-150°C, with a return water temperature of 70-90°C. The high water quality of the primary network significantly influences the effectiveness of insulation, impacting both the heating efficiency and the economic benefits of thermal operations.
Current Insulation Materials and Existing Issues in Thermal Pipeline Networks
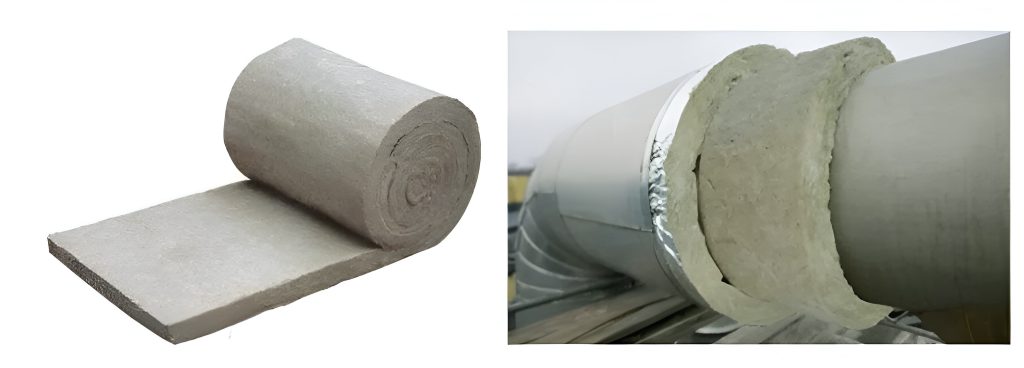
Currently, centralized heating pipeline insulation layers predominantly use materials such as rock wool and glass wool. Rock wool is an inorganic fiber made from natural rocks like basalt and pumice through melting and fiberizing. Glass wool, on the other hand, is an artificial inorganic fiber produced by melting materials like limestone, quartz sand, and dolomite into glass, which is then fiberized and processed with a binder.
The use of rock wool and glass wool materials poses several issues:
Poor Stability: After installation, the initial effectiveness meets design requirements. However, after several months of operation, radiative heat loss increases, leading to the gradual failure of the insulation layer. The soft nature of materials like rock wool and glass wool, relying on binders for cohesion, makes them susceptible to failure as the binders degrade over time. Additionally, vibrations caused by hydraulic shocks and pressure fluctuations in the pipeline result in material settling, creating an uneven layer. This settling can lead to gaps between the pipeline and the insulation layer, promoting convective heat exchange, which increases radiative heat loss.
Corrosion Under the Insulation Layer: The porous structure of rock wool and glass wool materials allows moisture to penetrate. When moisture infiltrates the insulation layer and reacts with the pipeline walls, oxidation occurs, leading to corrosion and leaks. Even glass wool materials treated for hydrophobicity cannot withstand long-term use in high-temperature and high-humidity trench environments.
Short Lifespan: Due to the rapid degradation of traditional insulation materials like rock wool, frequent replacement is necessary. Aging leads to increased heat loss, higher maintenance costs, and elevated safety risks, with replacements required every 3-4 years.
According to statistics, network losses in centralized heating processes can account for up to 5% of the total thermal production. The significant impact of poor insulation on network radiative losses necessitates the use of superior insulation materials to reduce energy losses, decrease coal and gas emissions at the source, and provide positive economic and social benefits.
Advantages of Using Aerogel Felt in Thermal Pipeline Networks
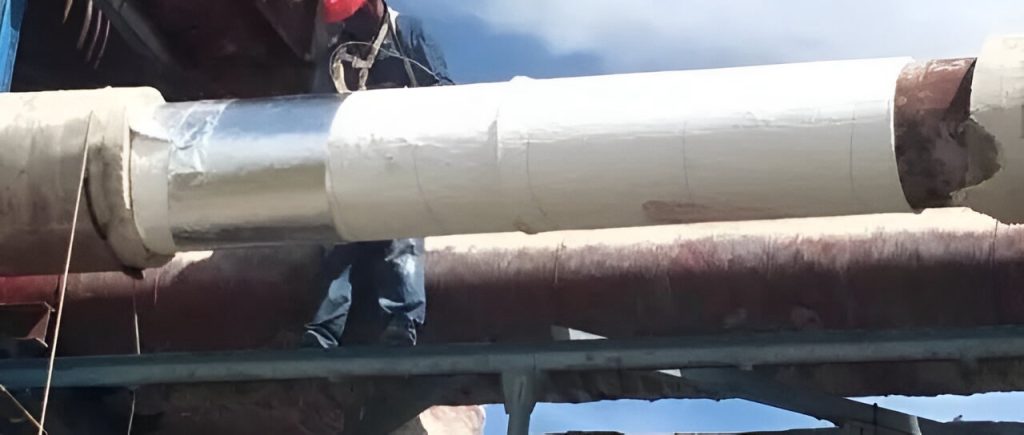
Excellent Thermal Insulation Performance: Comparison of thermal insulation performance indicators between traditional insulation materials and aerogel insulation material:
Insulation Material Rock Wool Felt Glass Wool Felt Aerogel Felt Thermal Conductivity at Room Temperature (25°C) (W/(m·K)) 0.049 0.044 0.020 Thermal Conductivity at High Temperature (300°C) (W/(m·K)) 0.0904 0.0831 0.036 Density (kg/m³) 60-120 50-120 ≤220 Maximum Operating Temperature (°C) ≤400 ≤300 -195~650 Hydrophobicity Poor Poor Good Lifespan (Years) 2-5 2-5 10-20 Higher Energy and Economic Efficiency: Taking a city’s primary heating pipeline as an example, when comparing 60mm glass wool and 30mm aerogel insulation for overhead installation with a DN800 diameter, the results are as follows:
Insulation Material Glass Wool Felt Aerogel Insulation Felt Insulation Thickness (mm) 60 30 Outer Diameter after Insulation (mm) 940 880 Supply Water Temperature (°C) 150 150 Heat Loss per Unit Length (W/m) 323.8 211.7 Ambient Temperature (°C) 20 20 Wind Speed (m/s) 0 0 Surface Temperature after Insulation (°C) 42.7 36.6 Energy Saving Rate (%) — 34.6 Using aerogel felt instead of glass wool felt not only reduces insulation thickness by 50% but also achieves an energy-saving rate of 34.6%.
Fire Resistance up to A Grade: The material itself contains almost no organic substances, and its combustion performance meets the A2 level requirements of GB 8624-2012, ensuring safety during installation and operation.
Reduction of Corrosion Under the Insulation Layer: As the material itself is free of chloride ions and exhibits extremely high hydrophobicity, with a water repellency rate exceeding 99.6%, proper sealing can prevent the accumulation of water vapor on the inner side of the insulation layer, minimizing corrosion beneath the insulation.
Long Lifespan: Aerogel insulation felt demonstrates exceptional resistance to aging and dimensional stability, providing a lifespan of up to 10 years, which significantly outperforms traditional materials.
Enhanced Operation and Maintenance Safety: For pipelines laid in trenches, limited space poses inherent dangers, with confined space operations carrying a high risk of asphyxiation and poisoning incidents. Compared to traditional materials like glass wool, aerogel felt, with its longer lifespan and stable performance, reduces material replacement frequency, effectively minimizing confined space operations and lowering the incidence of safety accidents, ensuring safe operation and maintenance.
Green and Environmentally Friendly: Aerogel felt uses silica as raw material, containing no toxic or harmful substances. It is a green and environmentally friendly material, similar to sand, and can be landfilled or recycled by manufacturers. In contrast, the large volume and short lifespan of inorganic insulation materials like glass wool impose significant environmental pressure.
In conclusion, aerogel insulation felt, with its outstanding comprehensive performance, can effectively replace traditional insulation materials such as rock wool and glass wool. It provides robust economic benefits and operational safety for thermal pipeline networks while promoting environmental sustainability. Its adoption in the thermal industry deserves widespread promotion and use.