Advantages of Aerogel Felt in the LNG Field
Current State of LNG Insulation:
In LNG engineering and other cryogenic projects, temperatures involved in low and ultra-low temperature equipment typically range from -40 to -170 degrees Celsius. The most commonly used cryogenic insulation materials include PUR/PIR, foamed glass, rubber and plastic, modified phenolic foam, etc. These materials represent a significant improvement in both performance and construction compared to the previously used perlite materials. The effectiveness of cryogenic insulation not only impacts the overall efficiency of the equipment but also plays a crucial role in ensuring the safety of the facility. Appropriate insulation materials not only reduce energy consumption and minimize refrigeration loss but also provide assurance for environmental compliance, ensuring safe production and creating better economic benefits. The emergence of aerogel-type insulation materials seems tailor-made for cryogenic insulation and is already widely applied both domestically and internationally.
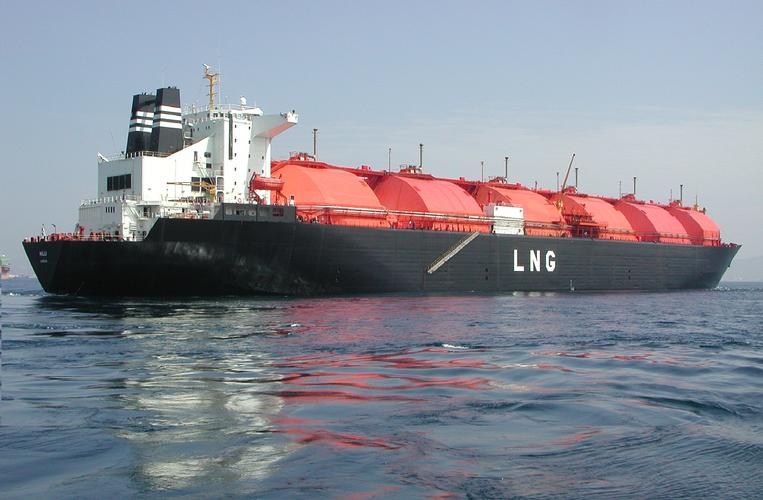
Current State of LNG Refrigeration:
- Traditional materials experience rapid deterioration in insulation performance, resulting in high maintenance costs.
- Inadequate insulation performance and significant refrigeration loss of traditional materials pose risks to the storage and transportation of natural gas or other compressed gases.
- Large thickness of traditional materials complicates the design of densely arranged pipelines.
- Poor insulation effectiveness leads to corrosion due to condensation on pipes.
- Excessive condensation water easily renders the insulation layer ineffective.
- Waterproof properties of organic materials are present but fail to meet fire protection requirements.
Advantages of Aerogel Super Material:
- Optimal low-temperature stability; can maintain refrigeration performance and excellent flexibility even at -200℃ without cracking.
- Outstanding dimensional stability; nanoscale special structure resists internal stress caused by pipeline expansion without the need for expansion joints.
- Excellent hydrophobicity of aerogel material effectively prevents water from penetrating the surface of metal pipelines, preventing corrosion and preserving insulation effectiveness.
- Inorganic material composition, primarily SiO2, without adhesives, ensures stable performance, safety, fire resistance, and an extended lifespan.
- Convenient material cutting and construction, resulting in low maintenance costs.
- Superior refrigeration performance; thermal conductivity at room temperature is only 0.018W/m·k, and at ultra-low temperatures, the thermal conductivity is <0.01W/m·k. This significantly reduces the required thickness of the refrigeration layer, effectively lowering refrigeration loss and optimizing the design of densely arranged pipelines.
Performance Comparison between Aerogel and Traditional Refrigeration Materials:
| Aerogel composite felt pad | Foam glass | Foam PIR |
Thermal conductivity | 0.010~0.020 | 0.050~0.080 | 0.030~0.040 |
Bulk density(kg/m³) | 190 | 150~240 | 50~180 |
Cold insulation thickness | 0.50 | 2 | 1 |
Water absorption rate(vol%) | 0.36 | 2 | 1.5 |
Waterproofness | Overall waterproofing, hydrophobicity ≥ 99%, nano structure | Poor waterproofing requires additional waterproofing measures | Poor waterproofing requires additional waterproofing measures |
Constructability | Can be rolled into rolls, shaped parts, with good flexibility and easy construction | Very poor, high loss | Normal, can be foamed on site, but the foaming uniformity is poor. |
Ultra low temperature stability | Excellent, expected lifespan 5-10 years | Moderate stability, with a lifespan of approximately 2 years | Easy to age, reduced strength, poor stability, replacement required from 6 months to 1 year |
dimensional stability | 0.45% | poor | poor |
Reusability | Reusable during disassembly and maintenance | Fragile during disassembly and unusable | Fragile during disassembly and unusable |
Economic Comparison between Aerogel and Traditional Refrigeration Materials:
Aerogel insulation blanket | Foamed glass | PIR | |
Expected Thickness of Insulation Layer (mm) | 40 | 160 | 80 |
Expected Surface Temperature (℃) | 30 | 30 | 30 |
Volume of Insulation Material (m³) | 17.5 | 140 | 45.2 |
Main Material Cost (in thousands of yuan) | 18 | 14 | 7 |
Construction and Auxiliary Material Cost (in thousands of yuan) | 3 | 8 | 5 |
Cooling Loss Situation | 约1/3 | 2 | 1 |
Maintenance Situation | Almost negligible, even in the case of physical damage. Easy to repair | Minimal maintenance required; after reaching the end of its lifespan, a complete replacement is recommended. | Significant aging issues; requires major repairs every 3-6 months, with maintenance costs ranging from 10,000 to 20,000 yuan per occurrence. |
Buried Pipeline | Small volume, if the earthwork project is one-third of the traditional prefabricated pipeline, it results in lower transportation costs due to the reduced volume. | The volume is too large, making it impractical for use as a prefabricated pipeline. | The volume is large, making it impractical for the production of prefabricated pipelines. |
Note: Calculations are based on a pipeline with a diameter of 100mm and a length of 1km