Applications of Aerogel Insulation Materials in the Pipeline Industry
Current Status of Pipeline Insulation:
In the present industrial heating pipelines, temperatures range from 50 degrees to 600 degrees. Silica-alumina magnesia materials and glass fiber materials are widely used in the insulation projects of these pipelines. Approximately 30 years ago, insulation projects almost exclusively employed rock wool and mineral wool materials. However, in today’s industrial insulation projects, rock wool insulation has been phased out. Despite similar construction and waterproofing performance, the primary reason for its elimination is the gap in thermal conductivity. The following are the thermal conductivity coefficients of various materials at different temperatures.
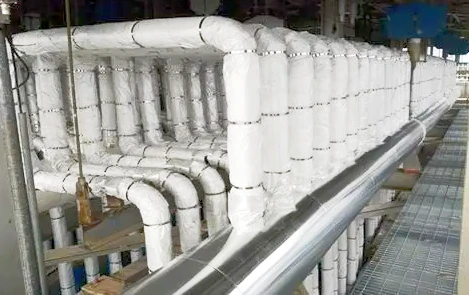
Current Issues in Pipeline Insulation Projects:
- Unreasonable insulation structure, non-standard insulation thickness, and inadequate insulation construction.
- Susceptibility to deformation, settlement, poor thermal stability, high damage rates, leading to poor long-term insulation effects that cannot meet process requirements.
- Ineffective insulation with a noticeable decline, causing increased maintenance costs for insulation projects and higher equipment operating expenses.
- Limited lifespan of only 3 to 5 years, requiring complete replacement at the end of its service life.
- Incomplete waterproofing, prone to water absorption and corrosion of the pipeline.
- For pipes with temperatures exceeding 100 degrees, the insulation layer needs to be at least >200mm thick, resulting in high thermal energy loss due to the high heat flow density of the pipeline.
Benefits of Aerogel Materials:
- Thermal insulation effect is 2-5 times that of traditional insulation materials, with more significant advantages at high temperatures, and a longer lifespan.
- Material is hydrophobic, effectively preventing moisture from entering the pipeline and equipment, and it possesses Class A1 fire resistance.
- Lightweight, easy to cut, sew, and adapt to various shapes of pipelines and equipment insulation, with less installation time and labor required.
- Reduced wrapping volume and lighter weight significantly lower the transportation costs of insulation materials.
- Provides sound absorption, noise reduction, and vibration damping functions while insulating equipment, improving environmental quality, and protecting devices.
- Only 1/2 to 1/5 of the thickness is needed to achieve the same thermal insulation effect as traditional materials, resulting in minimal heat loss and high space utilization.
Thermal conductivity mw/m·k | 25℃. | 100 ℃。 | 200℃ | 400℃。 |
Aerogel felt | 18 | 21 | 25 | 34 |
ceramic fiber blanket | 37. | 55 | 72 | 110 |
glass fibre | 42 | 50. | 70. | |
Rock wool | 55 | 70 | 92 | 140 |
Foam material | 36. |
Performance Comparison between Aerogel Composite Insulation Materials and Other Insulation Materials:
Aerogel composite insulation blanket | ceramic fiber | Rock wool | |
Thermal conductivity (at room temperature) | 18 | 36 | 55 |
Thermal conductivity at 350 ℃ | 30 | 110 | 130 |
Insulation thickness at 350 ℃ | 30mm | 100mm | 110mm |
Bulk density, kg/m3 | 200 | 128 | 110 |
Waterproofness | Hydrophobicity rate ≥ 99%, no special waterproofing measures required | Incomplete waterproofing, prone to water absorption, moisture absorption, and corrosion of pipelines. The surface of the protective plate needs to be sprayed with metal sealant for waterproofing | |
Insulation of tees and valves | Detachable insulation sleeve, with good insulation effect and convenient use. | The filling method or insulation box has poor insulation effect. | |
service life | 20Years | 3~5Years | 3~5Years |
Usage process | Good overall integrity, with good seismic and tensile resistance, and no particle accumulation, settlement or other phenomena during use. | The material structure is loose, and factors such as self weight, equipment vibration, and water ingress can easily lead to material disintegration and settlement, resulting in a significant decrease in insulation effectiveness and severe excessive heat loss. | |
Using Comparison | Using a smaller thickness can reduce the insulation thickness of the pipeline, reduce the spacing between steam pipelines, and reduce the area of the factory building | The insulation layer is thick, and there are easy gaps at the overlapping points. A higher expansion and contraction coefficient can easily make the gaps become thermal bridges, which are more obvious after vibration |
Economic Benefits Comparison between Aerogel Composite Insulation Materials and Traditional Insulation Materials:
Aerogel composite insulation blanket | Composite silicate felt | |
Expected surface temperature (℃) | 35 | 35 |
Insulation material thickness mm | 120 | 300. |
Total volume of insulation layer m ³ | 83. | 377 |
Main material costs (10000 yuan) | 85 | 45. |
Construction cost and auxiliary material cost (10000 yuan) | 11 | 20. |
Pipeline heat flux density (W/m) | 130 | 300 |
Heat loss ratio | 1 | 3. |
Total thermal energy loss (%) | 3% | 10% |
Note: (Example calculation based on a 1 km, 100 mm diameter, 300-degree heating pipeline.) In practical applications, the composite silicate felt’s insulation effectiveness will deteriorate after 2 to 3 months, leading to increased heat loss.